Robotlab - UR5e
Universal Robotics UR5e Cobots
UR5e robots are light-weight collaborative robot arms with 6 joints and can move a payload up to 5kg with submillimeter-level motion accuracy. E-series indicate the model is shipped with embedded force-torque sensor that could be used for certain taskes. There are so far 3 UR5e robots in the labspace connected to the lab network hub. This page provides a brief introduction on how to use the robot and program them with the lab or your own computers (often referred as remote computer). Refer to the official user manual for more extensive descriptions.
Basic Usage
The basic interaction with UR5e can be done via the teach pendant attached to the control box (usually referred as controller). Picture and instructions below show the basic steps to use it:
- Turn on/off robot controller: press the button marked in the picture.
- Robot status: Red - robot is not powered -> Yellow - robot is powered but not motors are not active -> Green - motors are active and can be commanded. Robot can only be moved while the status is green. Just use the button on the touch screen. A strand of sound of unlocking joint brakes will be heard while activating the robot, indicating it will be good to go.
- Open/Save controller program: open configuration or a control script to run. Note this is the script running on the controller not on the remote computer. In most cases, this is for loading a setup, e.g. IP adress of a remote computer, and scripts, e.g. ExternalControl, that the driver/library on the remote computer will talk to.
- Move robot: switch to the tab and use a GUI to move the robot upward/downward/left/right or each joint individually. There is also a home button to drive the robot back to the up-straight pose. Remember to shutdown the robot at the home position if the experiment setup wouldn’t be used for an extended period of time.
- Emergency stop button: smash it when the robot is moving in an unexpected way. This will mechanically brake and unpower the robot. It is always a good practice to put your hand next to it before running your program. Ask a peer for help when you could not due to other tasks.
- Settings: check and set various parameters, e.g. IP address of controller in the network. The address is needed for configuring the driver or the program to use on the remote computer.
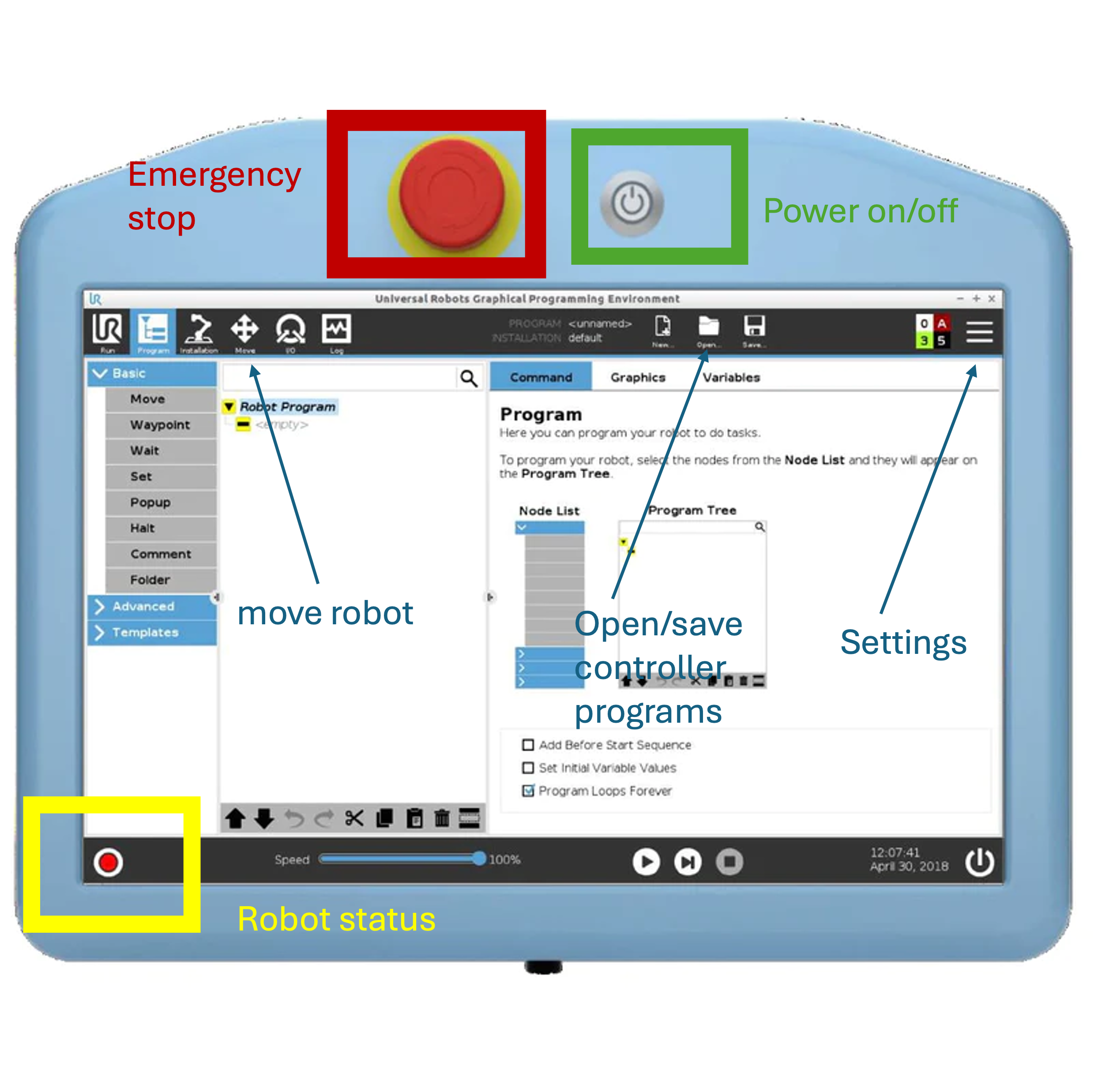
Progamming with UR5e
UR5e supports to run C++/Python programs on a remote computer via network connections. The connections can be a direct ethernet cable between controller and remote computer, or via a router/switch linking controller, remote computer and potentially other devices in a same network. It is recommended to use ethernet cable to connect laptop/workstation to the hub. WIFI may also be fine for certain applications but it can be unstable with a latency up to more than 100ms.
The C++/Python APIs are provided by a few libraries can be found online:
- Official ROS driver: this is an integral part of Robot Operating System (ROS) that will allow accessing a wide range of ROS packages for motion planning, sensor processing, diagnosis and visualization tools. You will need to install ROS on the remote computer (supporting Ubuntu/Mac/Windows, traditionally ubuntu is preferred). This is favoured for applications entailing communication across multiple processes on internal/external devices and heavy computation, e.g. you may want to distribute large neural network inference and real-time control of robots to separated computers.
- SDU ur_rtde: this is an unofficial wrapper of UR RTDE data protocol for users to quickly write C++/Python code. It depends on nothing more than basic Ubuntu programming toolchain. This is thus most suitable for small-to-middle scale tasks where only basic motion APIs and limited sensor processing are needed.
Note on real-time kernel: Both ROS driver and ur_rtde recommend to use a realtime kernel that would need recompilation or turn on some experimental feature on Ubuntu 22.04. This may be unnecessary unless cutting-edge performance is needed (UR5e can support a control frequency up to 500Hz). That said, one of the workstations in the lab has ROS driver with a real-time kernel compiled and configured. This will allow your application to communicate with this machine over ROS to control the robot. Ask the lab manager if this was needed.